In recent years, the oil and gas industry is one of the most active in terms of the implementation of artificial intelligence and machine learning. The pandemic crisis in 2020 has given impetus to accelerate digital transformation and technology adoption. In the oil and gas industry alone, AI was valued at $89 million in 2019 and is expected to have a CAGR of 10.14% from 2021 to 2026.
Already today, many companies experiment with modern oil and gas digital solutions to increase their efficiency and revenues. For instance, by using artificial intelligence in operations, corporations can develop more effective algorithms for drilling on land and the ocean floor.
Therefore, organizations worldwide try to make their exploration and production processes more efficient and streamlined, as well as reduce costs to the maximum while increasing profitability. Let's learn more about a particular use of AI in this industry – in particular, the implementation of predictive maintenance systems.
How Does AI Transform the Oil and Gas Industry?
- AI in oil and gas tools help companies digitize records and automate the analysis of collected geological data, which can lead to the potential identification of problems such as pipeline corrosion or increased equipment usage. As for machine learning, it allows organizations to improve productivity and performance as well.
- In general, AI has many applications in the oil and gas industry, such as optimizing production using computer vision to analyze seismic and geological data faster, minimizing downtime for preventive maintenance of oil and gas equipment, and reservoir understanding and modeling to predict oil corrosion risks for maintenance cost reduction.
- Also, AI helps companies carry out preventive maintenance of all available equipment. This allows them to extend the life of important elements of oil and gas production within the budget.
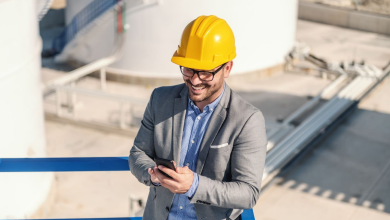
Directions for the AI Introduction in the Oil and Gas Industry
There are several directions in the development of AI in the oil and gas industry. They are divided into three categories such as emerging, accelerating, and maturing. You can see an explanation of these directions in the table below.
Emerging | Accelerating | Maturing |
AI-assisted cheminformatics |
Predictive maintenance systems |
Wellbore drilling optimization |
Sensor-guided flow mixing |
Smart factory applications |
Mixing ratio control techniques |
Intelligent embedded systems |
AI for workflow management |
Fuel transportation management systems |
Automated drilling tools |
Bio-fuel distribution management systems |
|
AI-assisted radiology |
||
AI-assisted CAD |
Predictive Maintenance Systems as The Main Tools for the AI Introduction in the Oil and Gas Industry
As you may know, in the extraction of oil, gas, and other minerals, a lot of equipment is involved, many of which operate automatically and are located in hard-to-reach places or regions with cold climates. Usually, it is hard and expensive to regularly inspect and maintain by employees, so monitoring and analytics systems for predictive equipment repair are in demand in this industry.
There are many definitions of preventive maintenance, but all such management programs are time-driven. In other words, maintenance tasks are based on elapsed time or hours worked, which are calculated with the help of statistical or historical information for various types of plant equipment.
The mean time to first failure, or failure rate curve, shows that new equipment has a high chance of failure in the first few hours or weeks of operation, which is usually caused by manufacturing or installation problems.
In the subsequent period, the probability of failures is much lower over an extended period of time. After this lifetime of the equipment, the risks of failure increase significantly with the number of operating hours. In preventive maintenance management, equipment checks, lubrication, repairs, or rebuilds are scheduled based on MTBF (mean time between failures) statistics.
All preventive maintenance management programs assume that equipment degrades after the time specified for its particular type. At the same time, the actual application of preventive maintenance varies considerably.
Some programs are very limited and only include lubrication and general tuning. More sophisticated ones also provide repairs, gear lubrication, adjustments, and rebuilds for all key equipment. Therefore, planning norms are a major determinant of these programs.
Top Companies That Implemented Predictive Maintenance Systems for the Oil and Gas Industry
The main suppliers of preventive maintenance systems in the world are such giants as General Electric, ABB, Honeywell, and Siemens. These companies sell not only equipment for the oil and gas industry but also preventive maintenance services to ensure their long life.
General Electric
General Electric provides predictive maintenance services for equipment that are great for specific applications or technologies such as digital twins. Their SmartSignal innovation allows businesses to diagnose and predict any equipment failure with maximum accuracy. In addition, this solution has helped many companies reduce maintenance and operation costs.
ABB
ABB's Ability Genix Industrial Analytics and AI Suite help organizations use artificial intelligence to minimize any risks and operating costs during oil and gas production. The supplier also offers preventive maintenance for all industrial equipment for oil and gas companies.
Honeywell
Honeywell provides its clients with an asset monitoring and analytics solution based on artificial intelligence. In this way, oil and gas companies can reduce the need for technical equipment and make their plants more reliable and safe.
Siemens
And finally, Siemens offers preventive maintenance services for industrial equipment, as well as solutions for optimizing the spare parts warehouse and accurate inventory accounting.
Conclusion
To sum up the above, preventive equipment repair implies the collection of predictive analytics of oil and gas from sensors installed on equipment, tracking and analyzing the parameters of its operation to identify maintenance periods and possible faults.
Such systems are necessary for any large company with a large fleet of equipment and facilities, which is expensive to maintain and regularly inspect by employees, while the cost of failure is very high.
What is the future of AI in oil and gas?
AI's future in oil and gas looks bright, refining exploration, drilling, safety, and operations. Through predictive maintenance, real-time analytics, and automation, AI will boost efficiency, cut costs, and lessen environmental effects, playing a key part in the industry's digital shift.
What are the technology trends in the oil and gas industry?
Oil and gas tech trends include digital twin simulations, IoT monitoring, AI-driven predictive maintenance, automated drilling, blockchain supply chains, renewable energy integration, and carbon capture. These innovations focus on industry efficiency, safety, and sustainability.