Recently, logistics has seriously changed in its technological means and has undergone major progress. If in the recent past, many processes were executed for a long time and required considerable labor inputs, now it is impossible to imagine the future without the extensive use of software and many innovative technologies.
Robotics in logistics is a technology that can provide the entire industry with huge potential. Robots are already used in many different areas, where they prove themselves to be efficient and reliable. Many innovative technologies require the use of robotics as there is a growing demand for automation, but the industry of logistics needs to be ready for such rapid changes.
The robots are accurate, they work quickly and minimize risks associated with human labor. But in what cases is it best to use robotics and how to apply them most effectively? We will discuss these aspects in this article.
What Are Logistics Robots?
Robotic technologies are mainly used in logistics for boosting the effectiveness of a company's work, minimizing risks, and avoiding errors. But these are not all the advantages and features that this tool has. Robots in logistics are divided into several types – from automated guided vehicles (AGVs) to drones and are used in a number of areas where they have already proven their effectiveness and accuracy.
Now, with the growing influence of various innovative technologies in response to the challenges of the outside world, robots are becoming more and more popular, so we should be very familiar with their applications and the benefits they bring.
Which Robots Can Be Used for Logistics?
There is a range of robotic technologies that are commonly used in the logistics industry. Since warehousing is a very complex activity that involves many minor processes, robots are irreplaceable. The main goals for which logistics robots are used are streamlining multiple processes and ensuring safety. Therefore, different types of robots are used for different tasks.
From autonomous mobile robots to industrial robotic arms, these tools are used in many different areas of logistics. Automatic truck loading and unloading systems are usually implemented in product receipt and dispatch, as these two processes of warehousing include the largest number of movements. Industrial robotic arms are generally used in order picking, and drones are leveraged for delivering orders by air. All of these technologies allow faster, more effective logistics processes and reduced costs.
What's the Current Situation with Robots in Logistics?
Experts believe that in the future, robots can provide indispensable assistance in automation and streamlining of operations and become a truly integral part of warehousing. The joint work of people and robots is considered the most effective in the logistics industry. It gives companies a huge potential as robotic tools can perform enormous amounts of work compared to employees, and new technologies are constantly emerging. It is logical to assume that in the future, robots will be everywhere in the industry, as such they present numerous opportunities for enhancing the productivity of work. In addition to being important for heavy workloads and large numbers of tasks, robots also play a critical role in complex transportation processes, for example, in the shipment of goods during the last mile.
As the entire logistics industry moves towards automation, robots will be involved in more and more processes. In addition, in recent years, the need for contactless delivery has greatly increased, which is why companies have begun to pay more attention to new technological tools. As a result, progress has gone even further.
It is believed that in the future warehouses will no longer do without robots and that these tools will be used in an increasing number of processes because the possibilities of robotics are enormous. Since this really offers a huge potential for improving the quality of logistics processes, companies are already looking for ways to use robots as efficiently as possible.
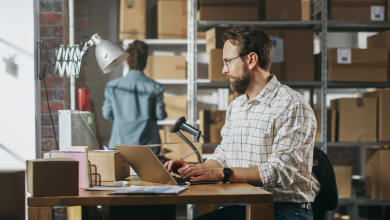
What are the Benefits of Adopting Robotic Logistics?
Robotic technologies implemented in the logistics industry have many advantages which include:
- a higher level of security;
- reduced human error;
- high productivity;
- enhanced work accuracy;
and so on. Among other things, robots can reduce costs, which can be a significant advantage for a company's finances. You can significantly change the number of expenses using robotic technologies.
If your employees do not have to perform large amounts of work and spend a lot of time and effort on it, this will contribute to higher employee satisfaction, which is also important for your company’s general performance. In addition, robotic tools and their efficiency help achieve a higher level of safety. This is important for ensuring security in the company, as well as for reputation. Warehouse automation also allows you to save big amounts of space and reduce labor costs, contributing to your better financial performance.
Warehouse Robotics in Supply Chain
1. Autonomous Mobile Robots (AMR)
These tools are designed to help deliver inventory all over the warehouse. Autonomous mobile robots are smart devices that identify the information on packages and sort them with precision and accuracy. This allows to significantly improve the productivity of work.
2. Aerial Drones
Drones have become a thing in logistics during the last few years. Thanks to their convenience, these tools are used for optimizing warehouse processes. Drones are able to quickly scan inventory and inventory space and provide accurate data to your software. Also, because drones are easy to use and move quickly, they don't take up much space in your warehouse and help in hard-to-reach areas.
3. Automated Guided Vehicles
Automated guided vehicles, or AGVs, assist transportation companies in transporting inventory. In large warehouses, they follow a track laid inside the space and move inventory. Among the significant benefits of AGVs, there is their high efficiency and substantial time savings due to their precise work.
4. Automated Storage and Retrieval System (AS and RS)
Both Automated Storage and Retrieval Systems are used for automatically storing or retrieving loads from storage locations. There are different types of As and RS depending on tasks, needs, and the items they need to work with. They can also be designed as cranes that retrieve various goods. One of the main benefits of using automated storage and retrieval systems is that it saves a lot of time and effort for employees, thus boosting the effectiveness of a company's work.
Conclusion
As the industry evolves and we cannot avoid the growing popularity of robotics, we need to get familiar with this kind of technology to implement it properly in our work and get the most out of its usage. The number of robotic technologies currently available on the market and their wide capabilities allow you to make the right choice in favor of the most productive work for your transportation business.
Robotic technology has a number of important advantages, such as better safety, higher precision, higher productivity, and so on. Through the implementation of robots in your work, you will be able to handle much more work and increase the satisfaction of your employees. Take advantage of the opportunities that the market offers and be able to do more in a short time.
With the help of robotic tools, you can save important resources such as time, the efforts of your employees, and money. By performing heavy and time-consuming processes with the help of robots, you can use efforts more intelligently and increase efficiency by trusting employees with more complex tasks. In addition, your employees will be less tired, and the accuracy of operations will increase. The accuracy of processes will affect safety and minimize unnecessary risks. You will protect your employees and avoid possible financial losses.
